Ball Bearing Catch Check
A manufacturing had temporary funnels that are suppose to detect and catch ball bearings. Though these funnels had issues regarding detecting if a ball bearing was missing and sometimes gets stuck without the ball bearing reaching the sensor. New Funnels were designed that contain fiber optics sensor.
- First image is the installation of the funnels on the line
- 2 Funnels were designed both having a DFF (design for future) if the fiber optics sensor ever failed a ring sensor can be added at the bottom.
- All parts including the funnels were modeled, tolerance in SolidWorks and then 3D printed on a FDM printer
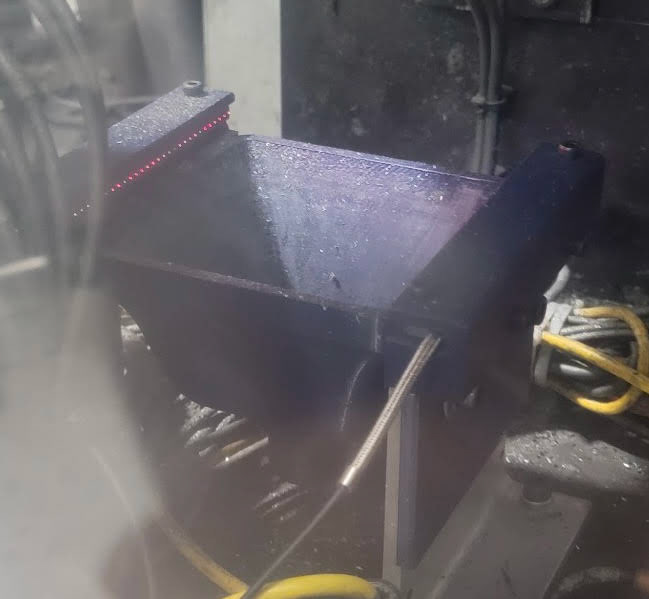
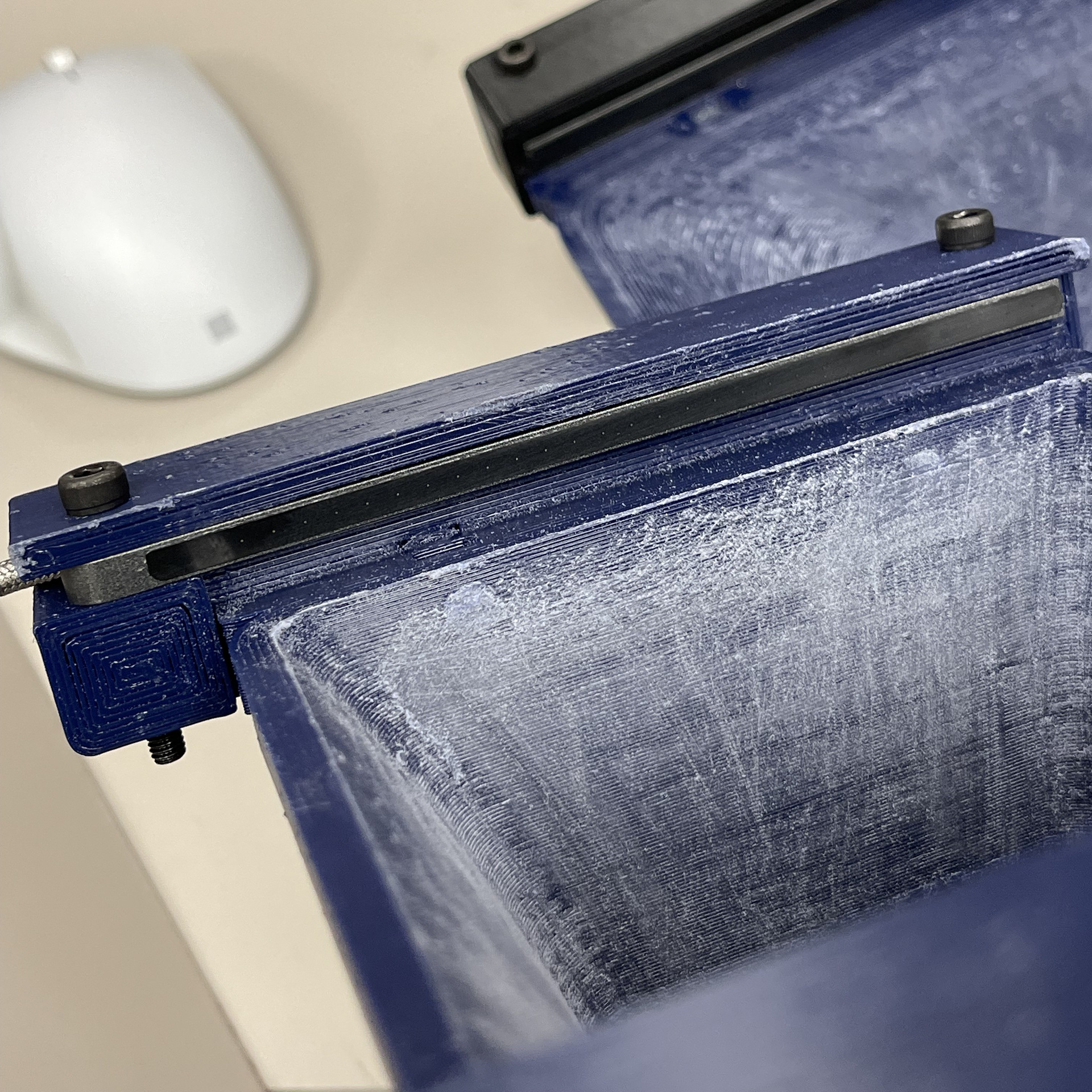
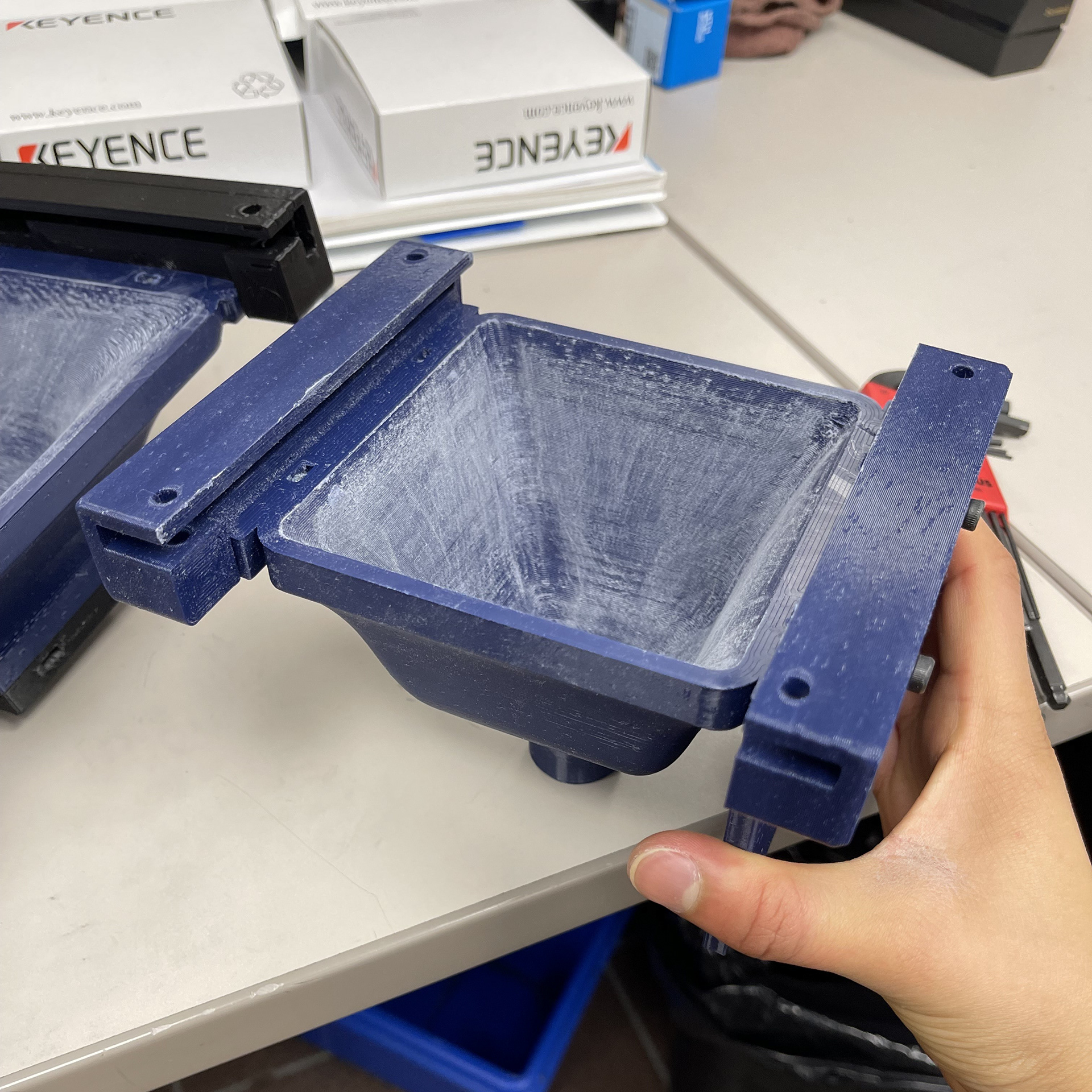
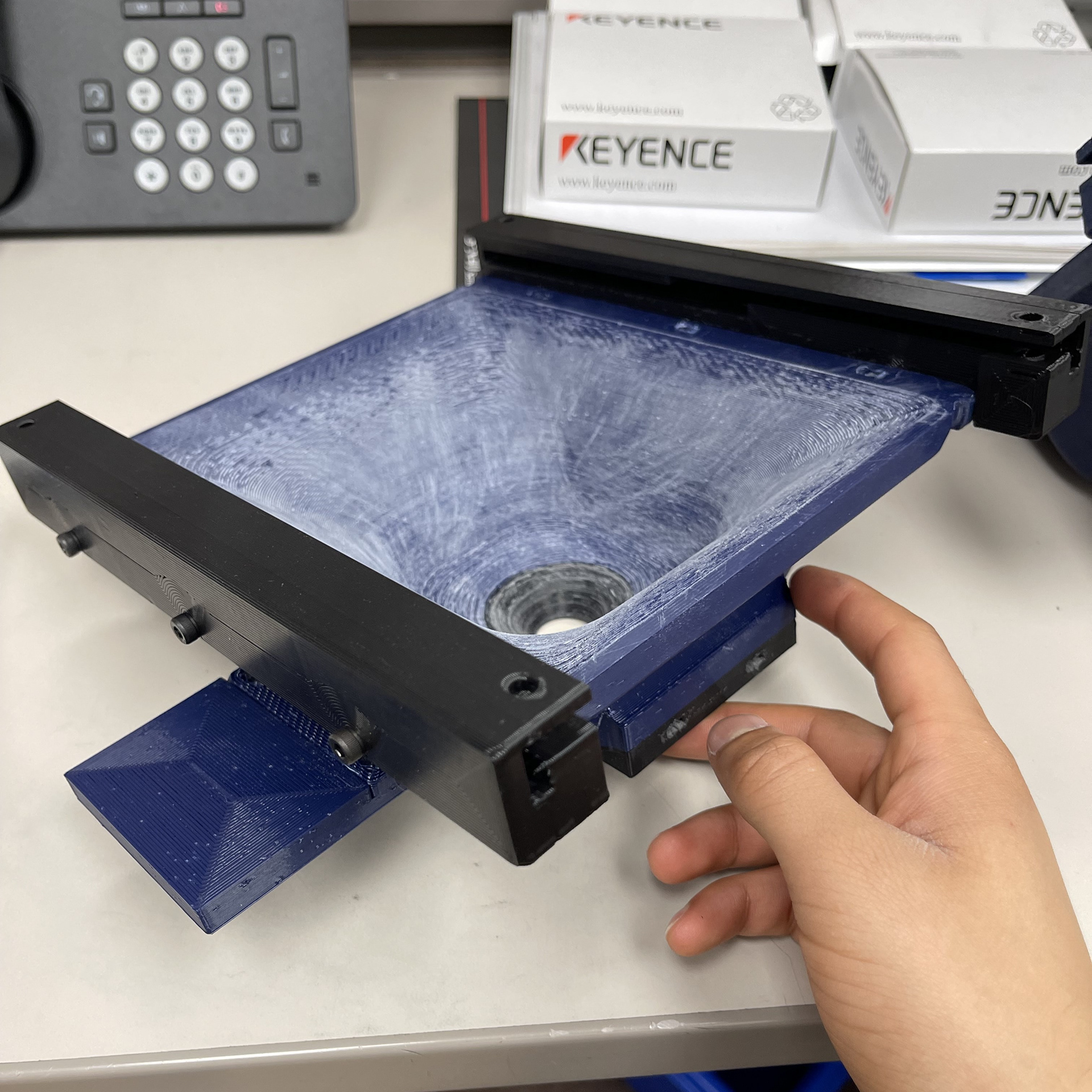
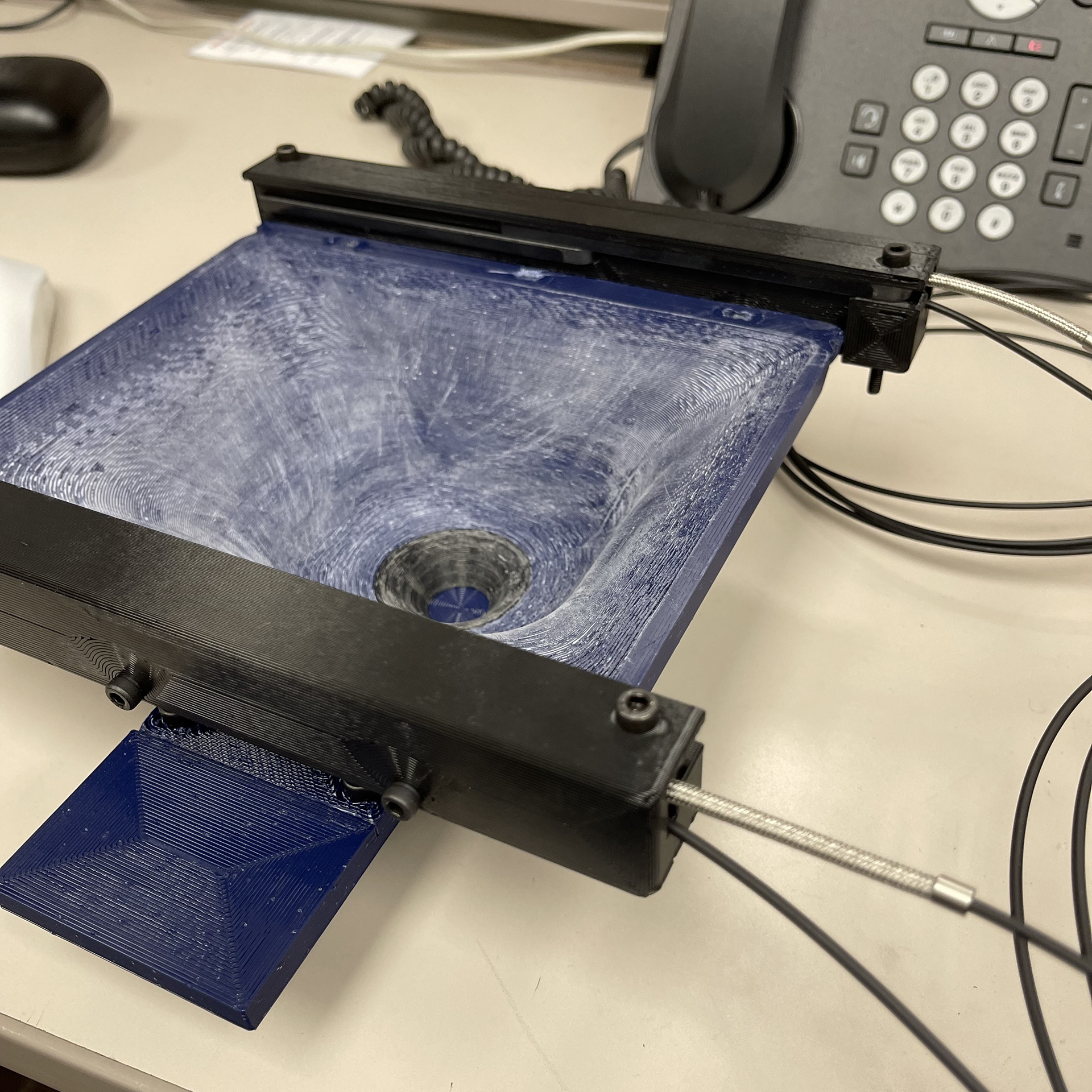
Spoiler Hinge Jig
This Spoiler Hinge was a product we were working on for a client. There were various alignment issues which was setting it to the correct height and having the top plate align parallel to the bottom which this in particular have us a lot of issues. the parallelism for plate would be off .5-.7 mm. So I designed a jig to address these issues.
- Front plate of the jig fixes the parallelism down to .2-.3mm off which was inline of what we wanted and successfully being able to hold that tolerance. Along with it allowing of 2 points of clamping
- Bottom plate perfectly made to allow for the correct height of the hinge to be set
- the opening of the Jig also allowed to adjust the screw with a tool which can be seen in image 1
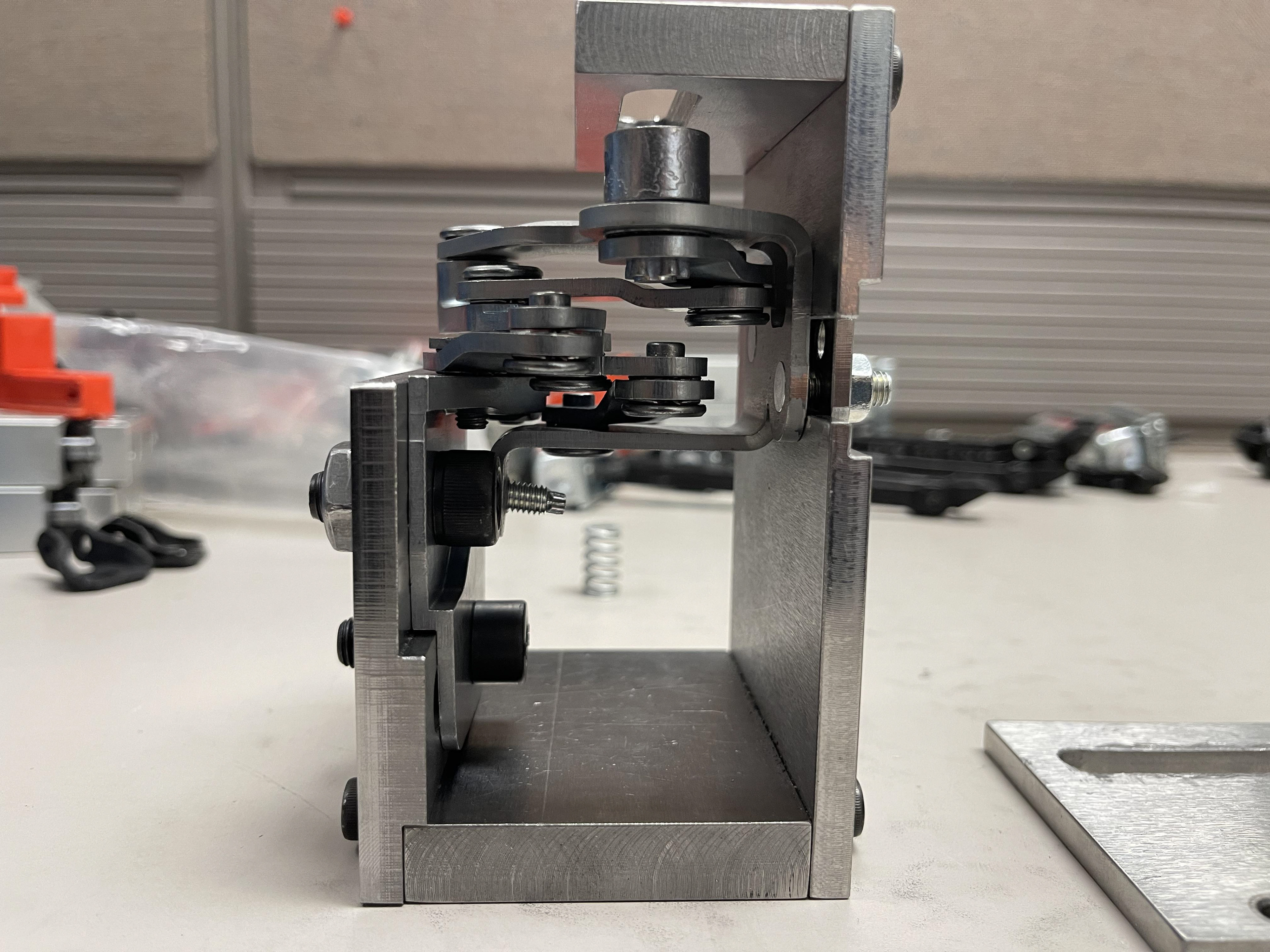
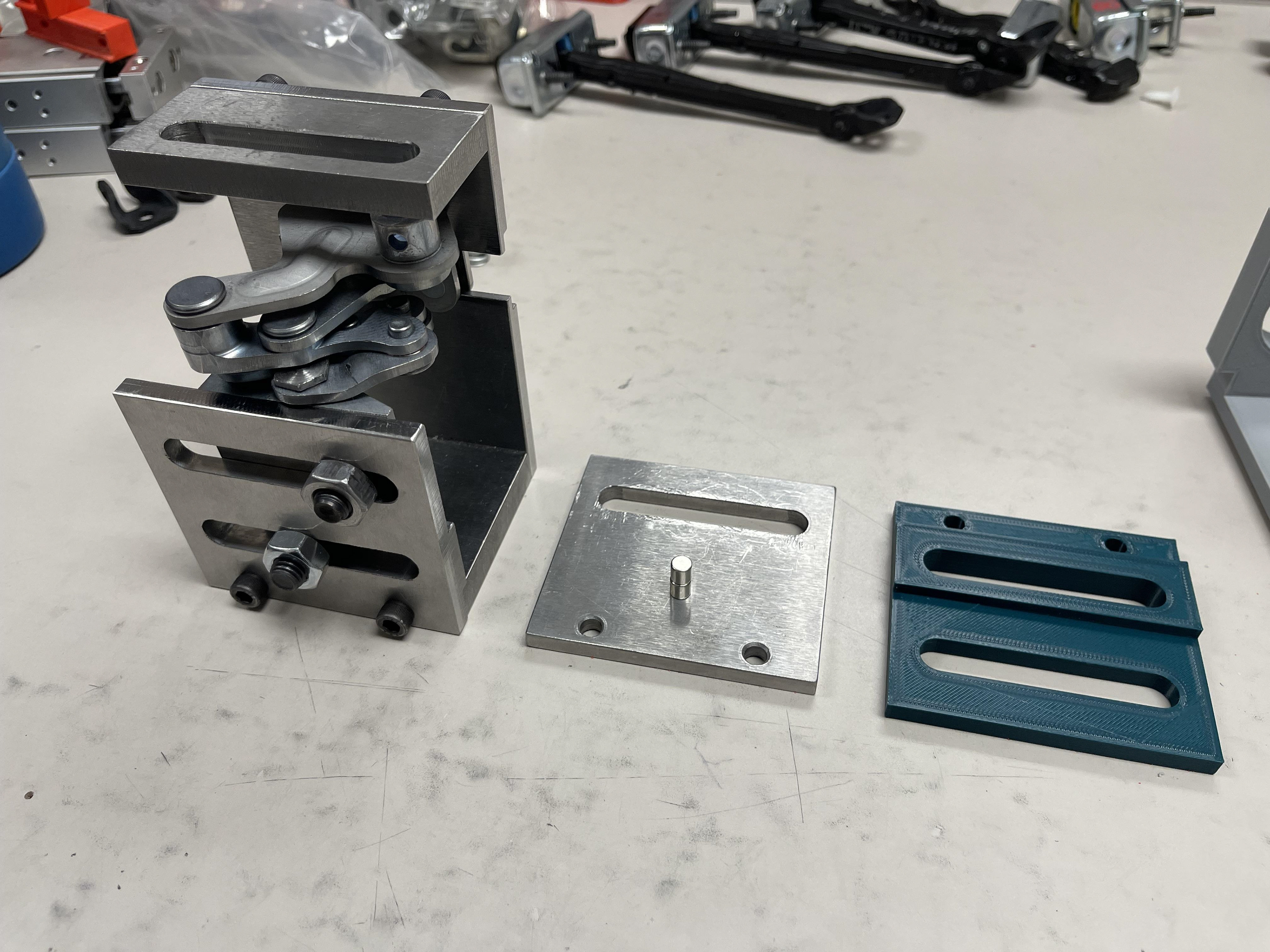
Roller Rack Frames
A new Manufacturing line was coming in for a new client that we were working with and that mean we needed a way for works to safely carry totes that contain the parts needed to make the product with out them hurting there backs. So various roller racks were made to accommodate for that. the bottom racks act as the main parts rack and once the tote is empty they will go on the top rack.
- All racks were first modelled in SolidWorks and technical drawings were made accordingly and was sent out to a fabricator for roller rack frames to be made
- Height of each rack were set accordingly to ergonomic standards
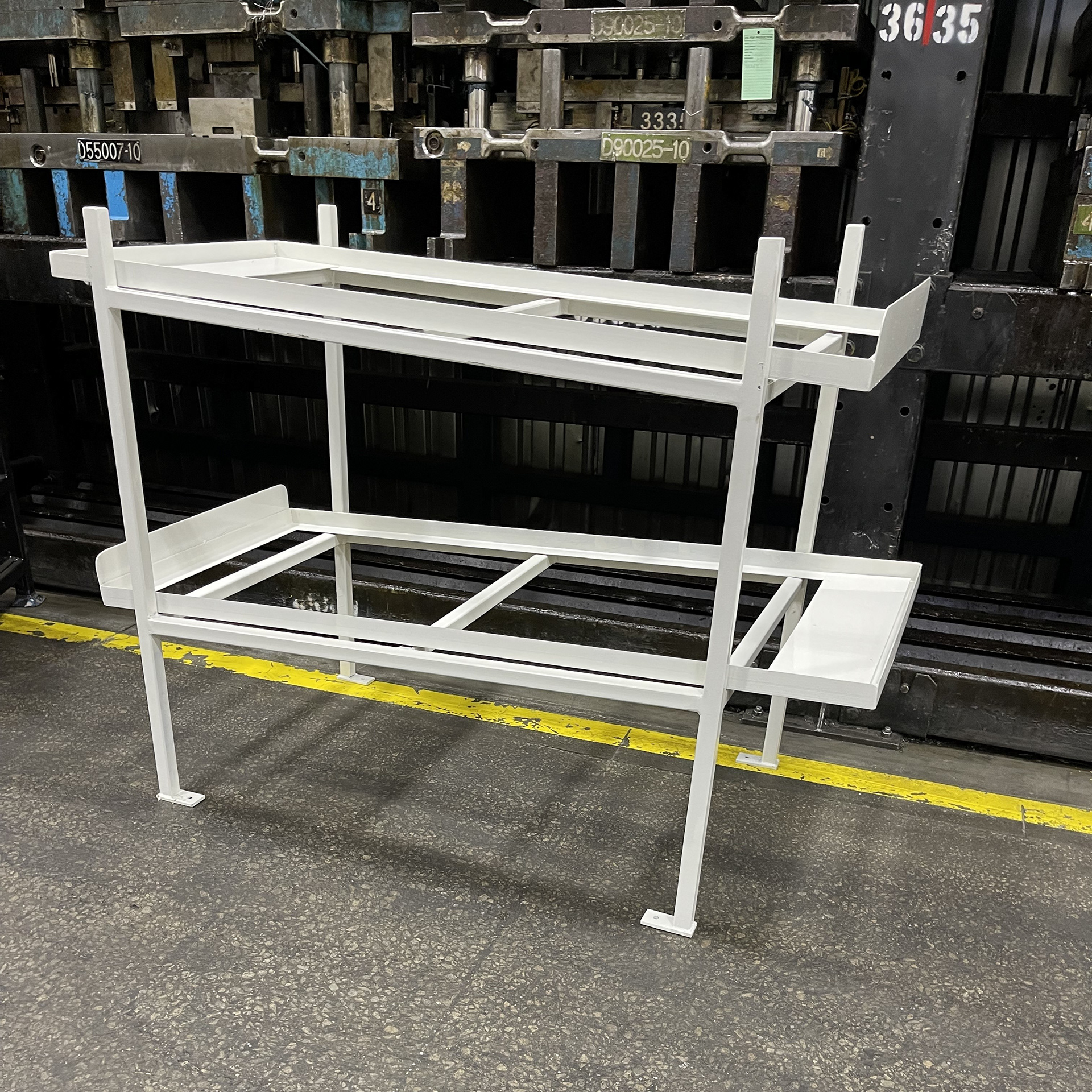
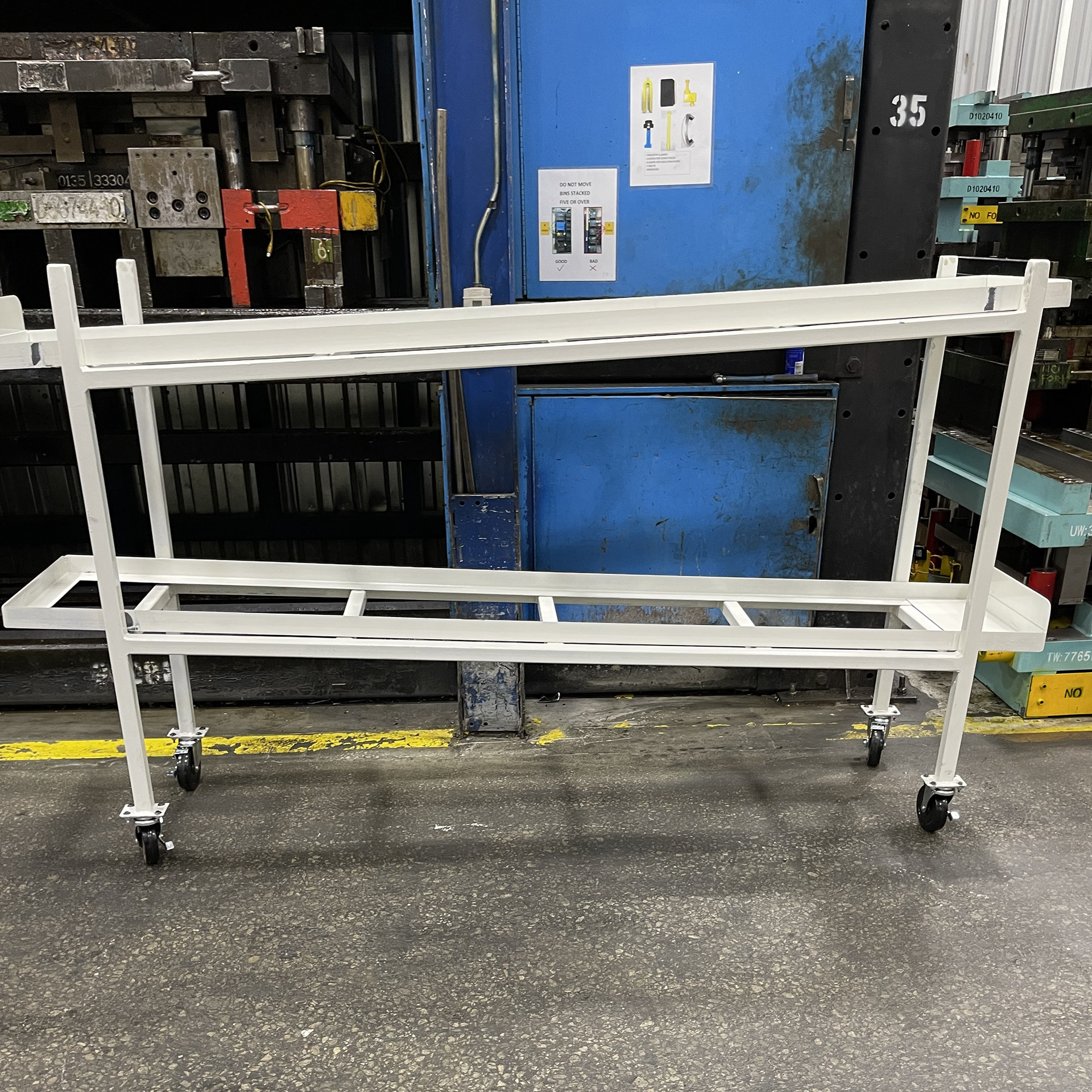
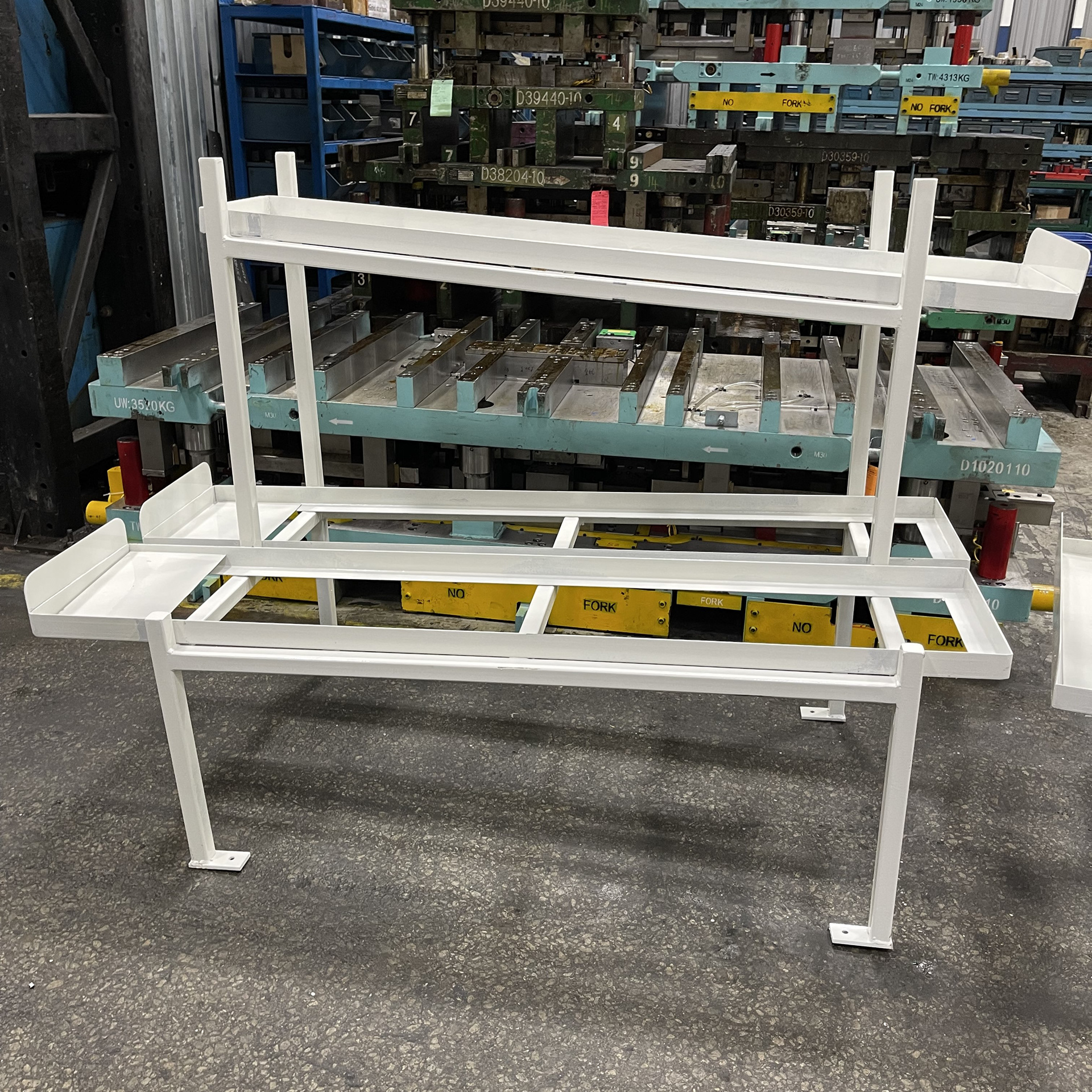
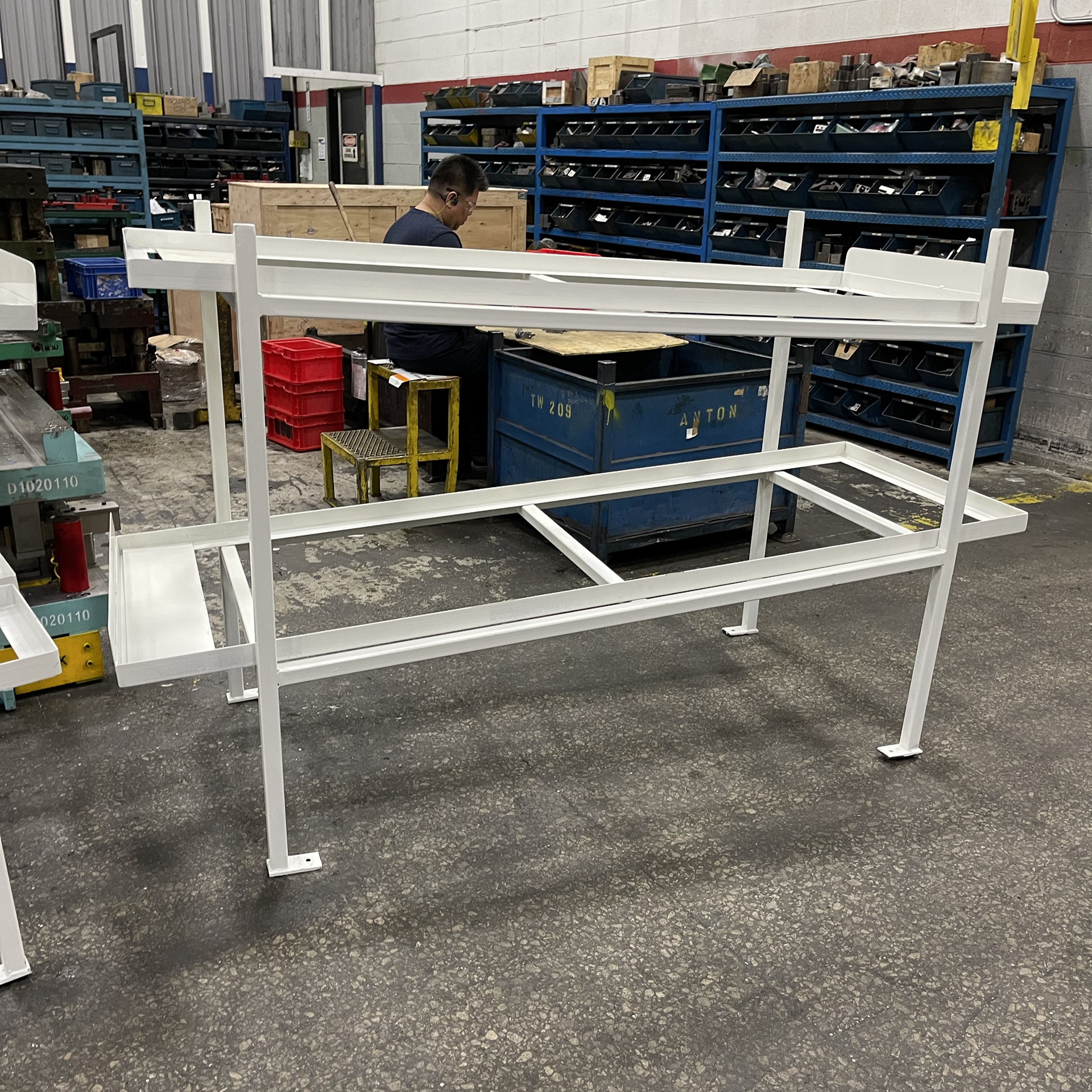
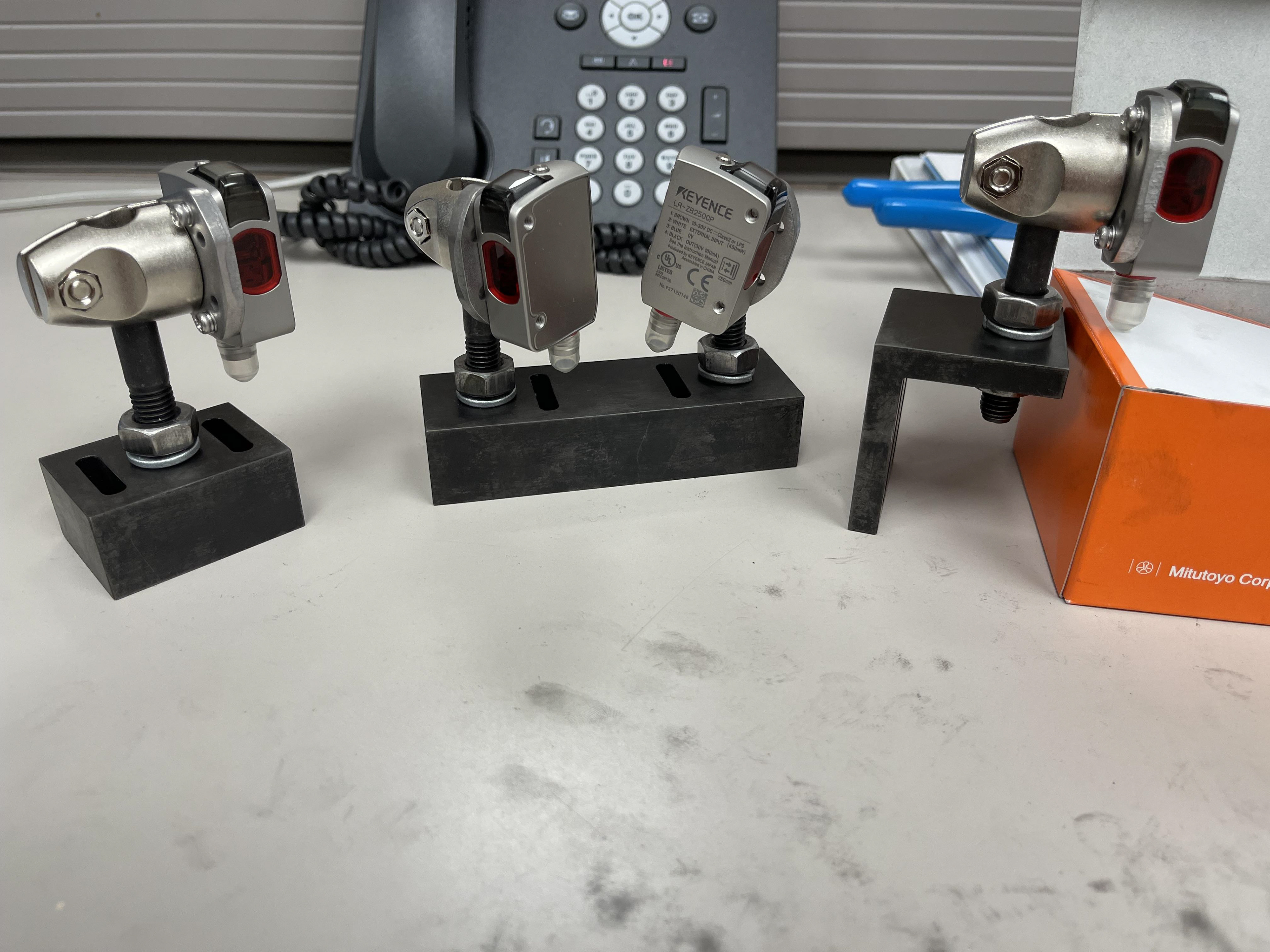
Through Beam Sensors
Sensors were needed replacing on one of the manufacturing lines as it had issues detecting a object that comes down the line and the current ones were designed and being interfered during its operation.
- Base mounts were modeled along with technical drawings made sent out for it to be machined
- Sensors and sensor mounts were outsourced from Keyence
All parts were modeled in SolidWorks and test fitted
Sorter Jig
There's a line on the floor that sorts hinges for any defects in terms of finally position and correct orientation of parts. They had an existing product they run on a different manufacturing line but didn't have a sorter jig for that specific hinge so I had designed one in SolidWorks and 3D printed to test fit before sending it out to be machined.
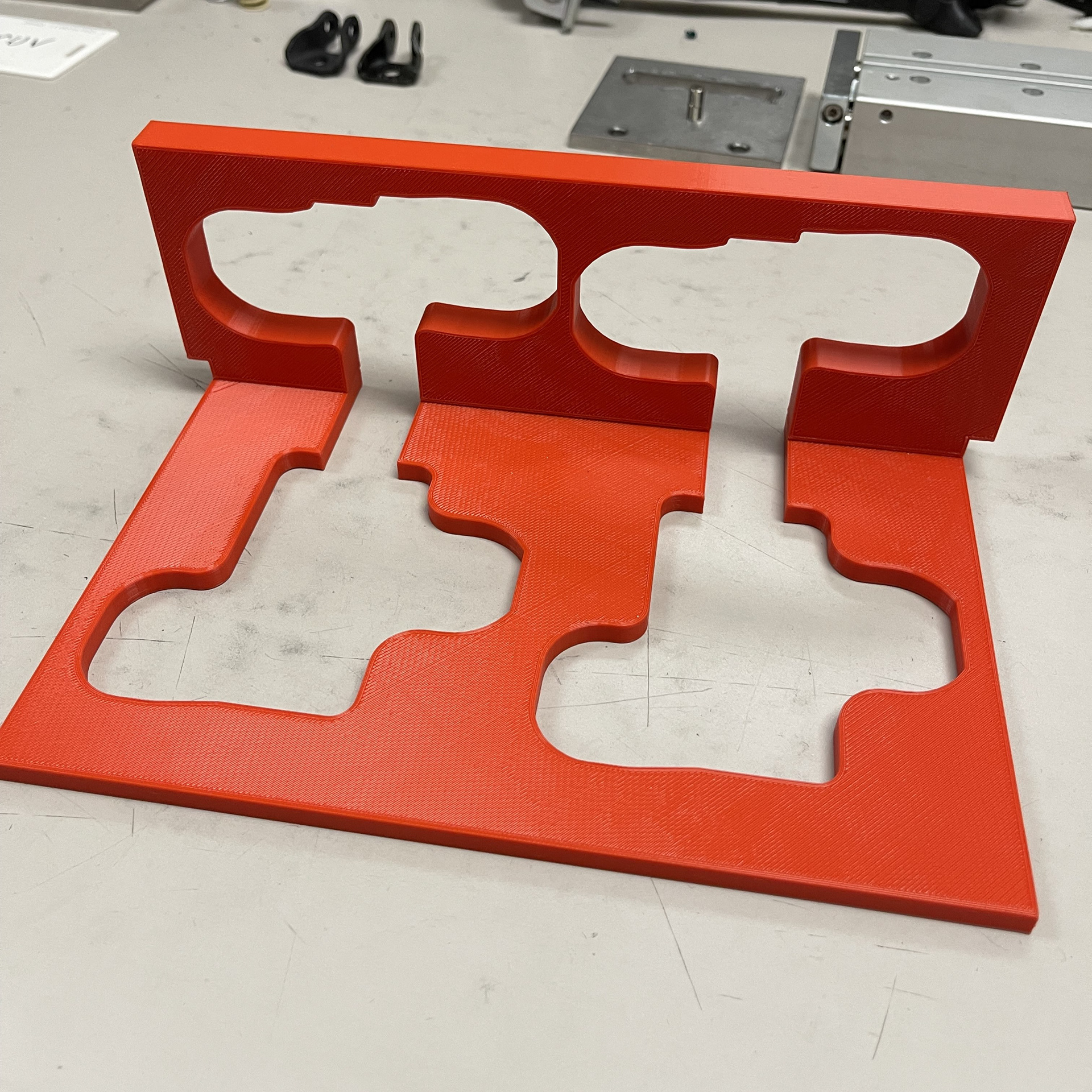

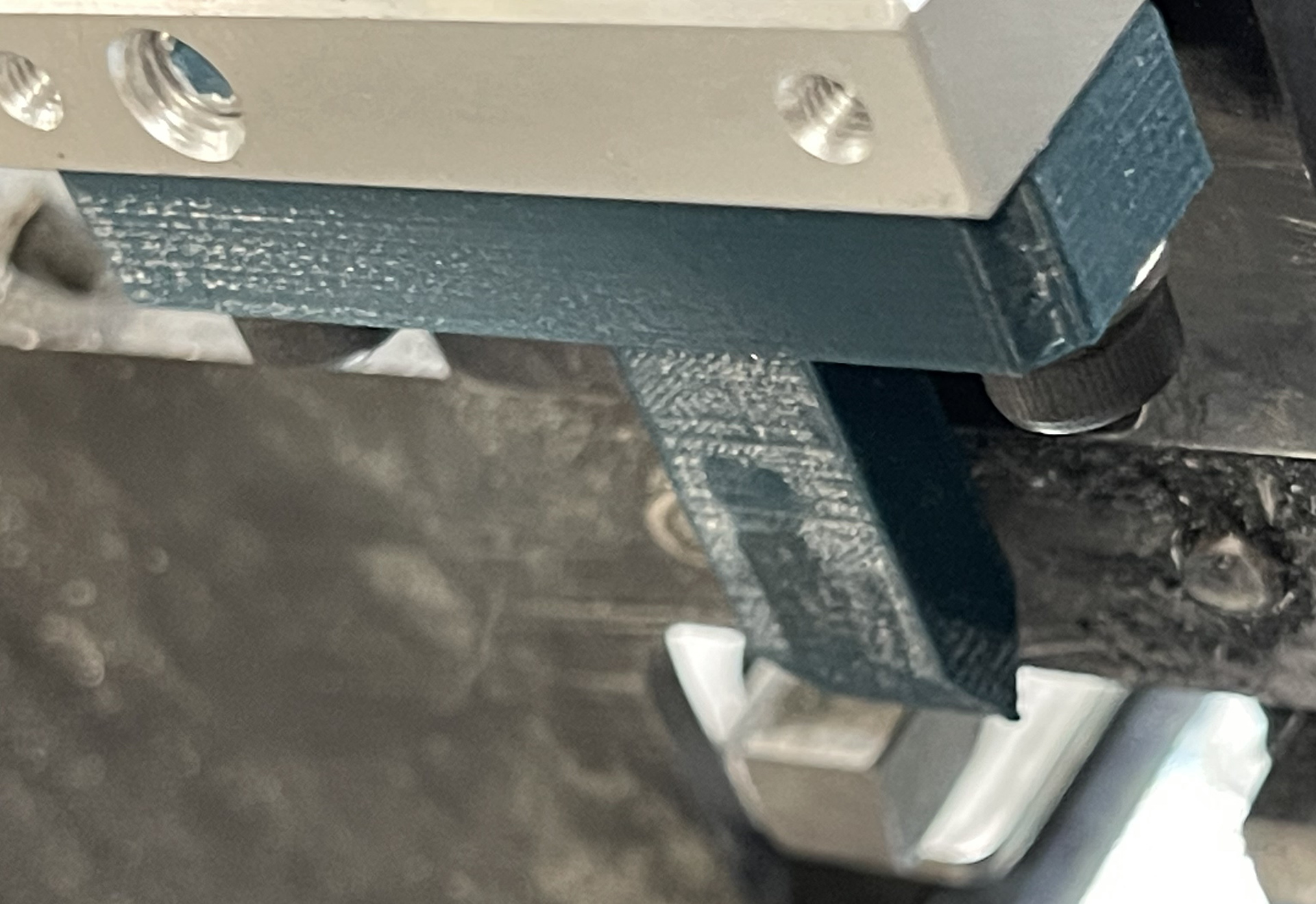
Check Tooling
A manufacturing had an issue regarding a check station that checked the presence of a ball bearing but the issue with that tooling was that it caused the ball bearing to be pushed out leading to final products missing it. So I had redesigned the tooling in SolidWorks and 3d printed the tooling have larger angle at the end that came to a point which meant it would keep the ball bearings in place and even if they were to pop out it would be pushed back in.