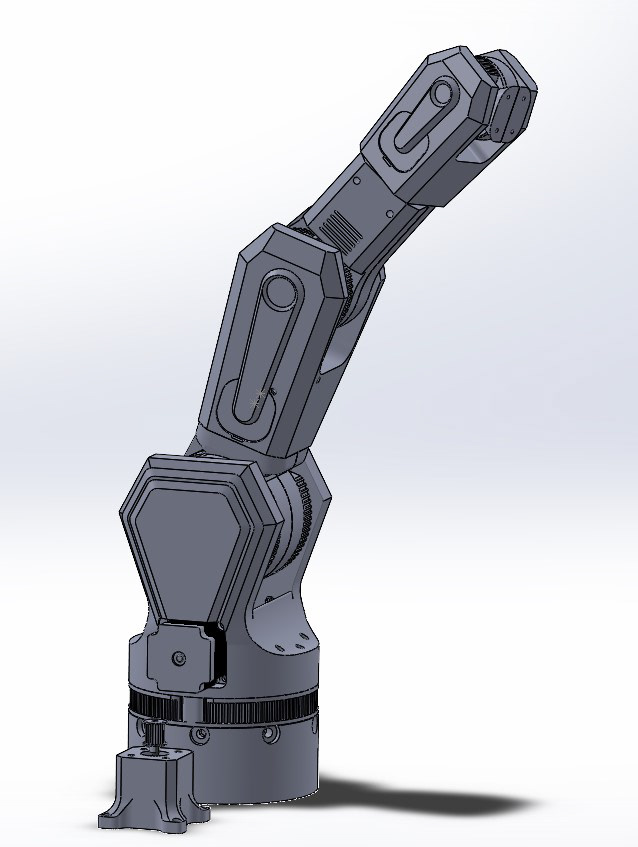
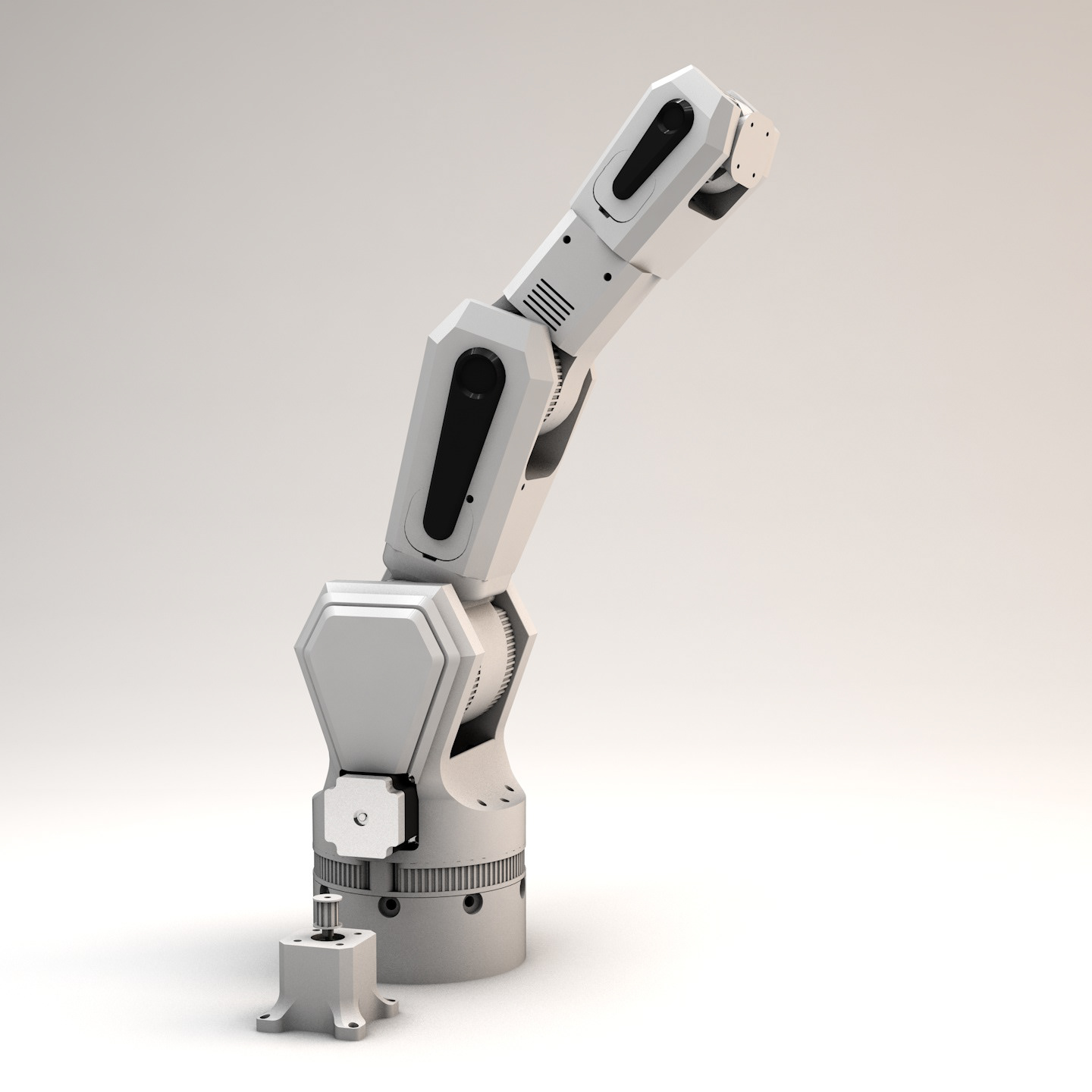
Design Changes
- Mechanical improvements for cross-sections of each axis
- Change in stepper drivers that can handle high currents and large stepper motors
- Tolerances changed for mechanical components to be better fitted
- Coverings made for exposed areas to reduce possibilities of debris getting in the mechanical system
- Visuals outer look changed to be more robust allowing for better stability
All parts were remodeled in SolidWorks and test fitted
3D Printing
All components were 3D printed using an FDM 3D printer in which PLA was chosen as the desired material as it had great mechanical properties like tensile strength. Components went through a post finishing process of sanding and painting for a quality look.
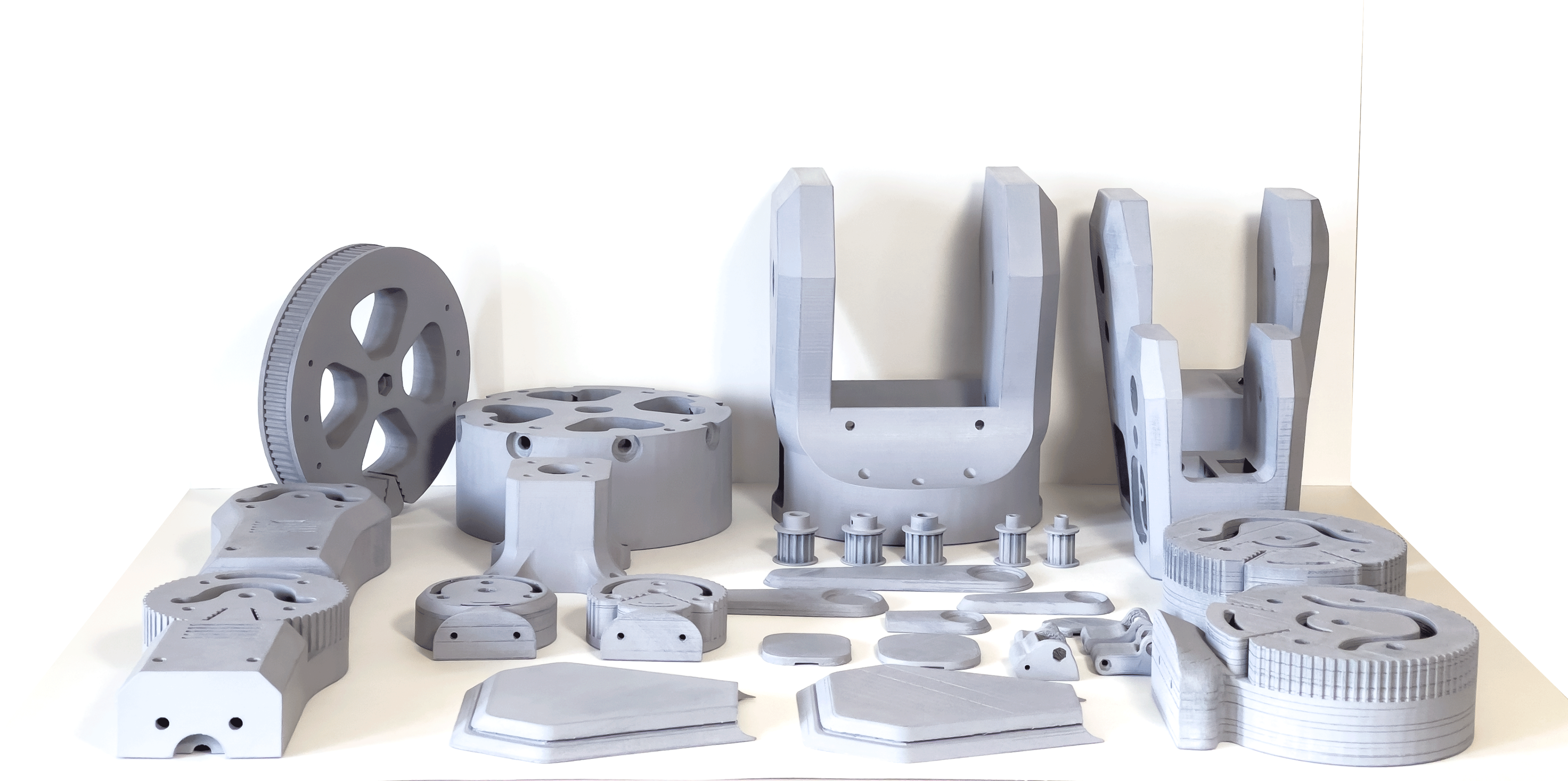
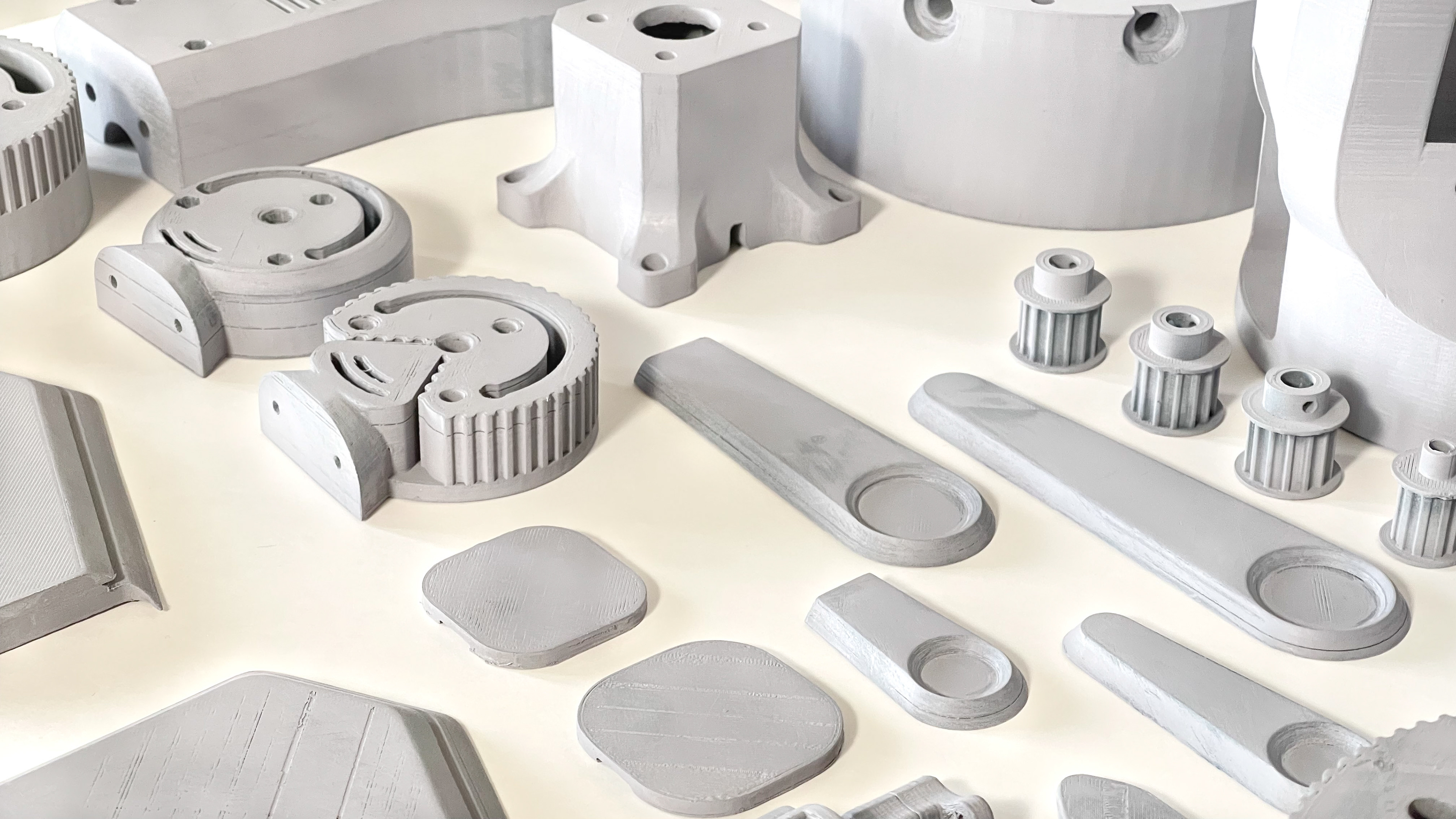
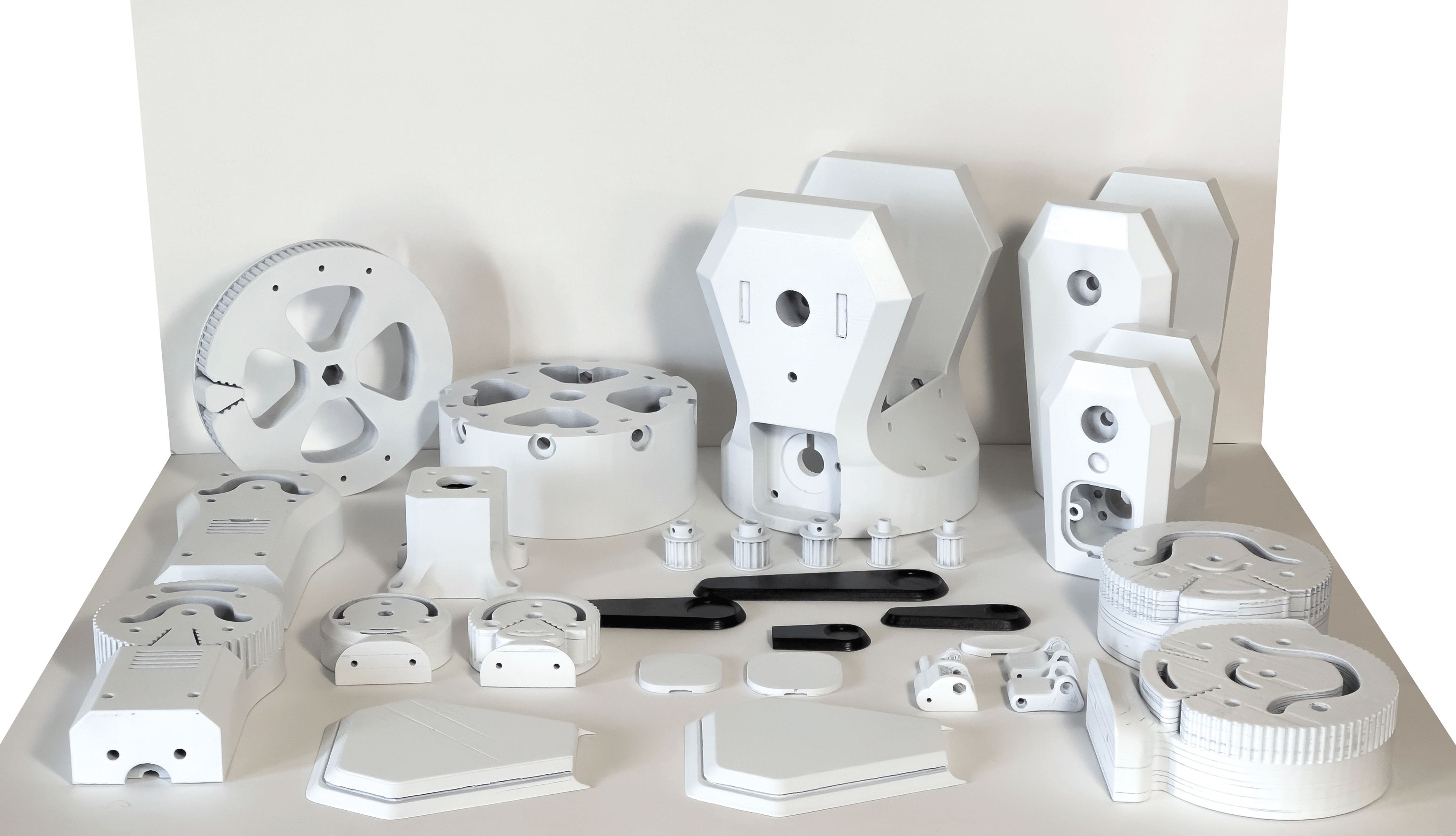
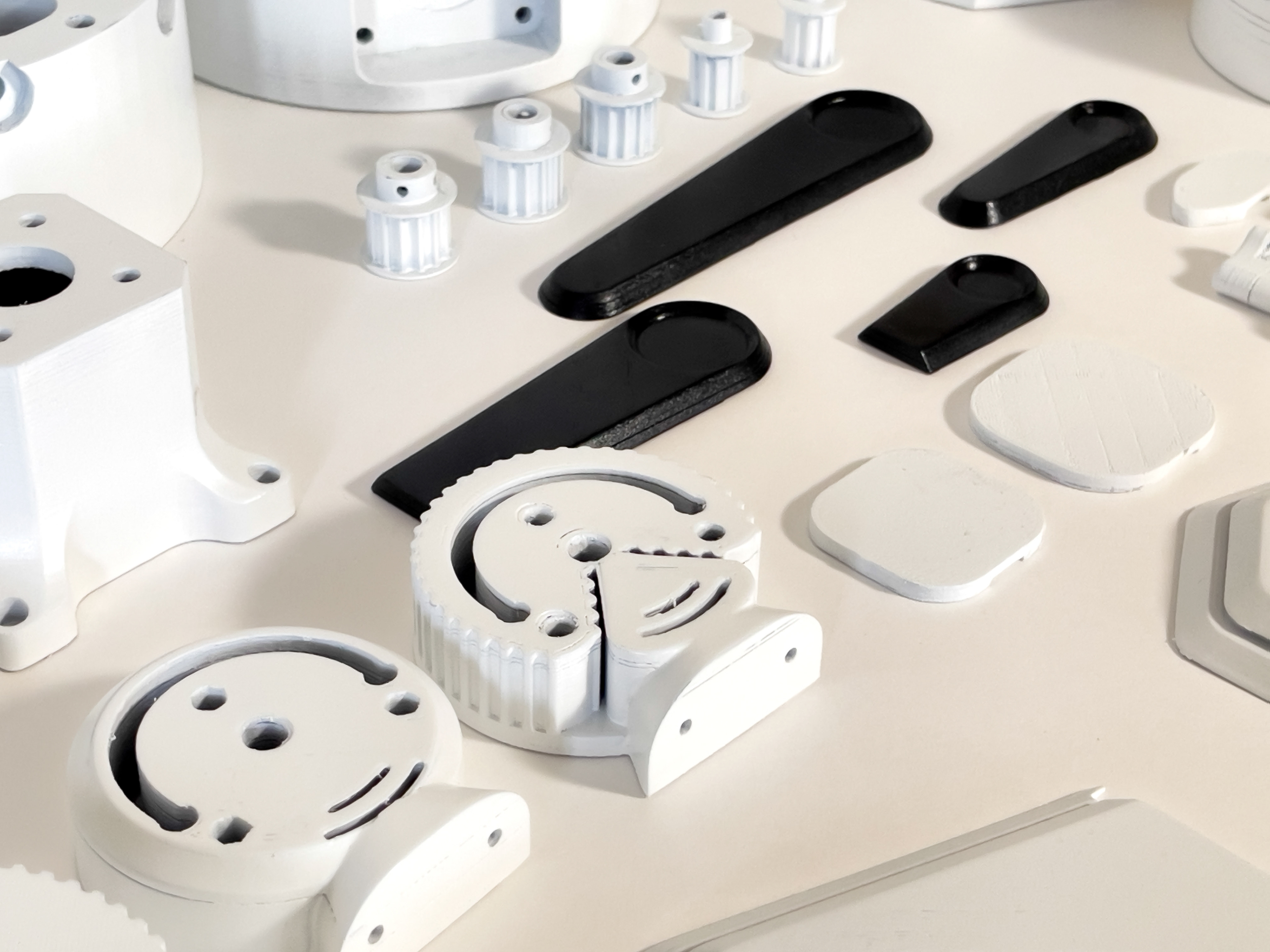
Wiring/Electronics
Electronics
- 24-volt power supply is used which is preferred for stepper motors to run smoothly
- DRV8825 drivers are used to driving the stepper motors which can handle high currents and provided a more compact form
- Ramps 1.4 board was modified to handle 24 volts by replacing the poly fuses with automotive fuses
Final Construction
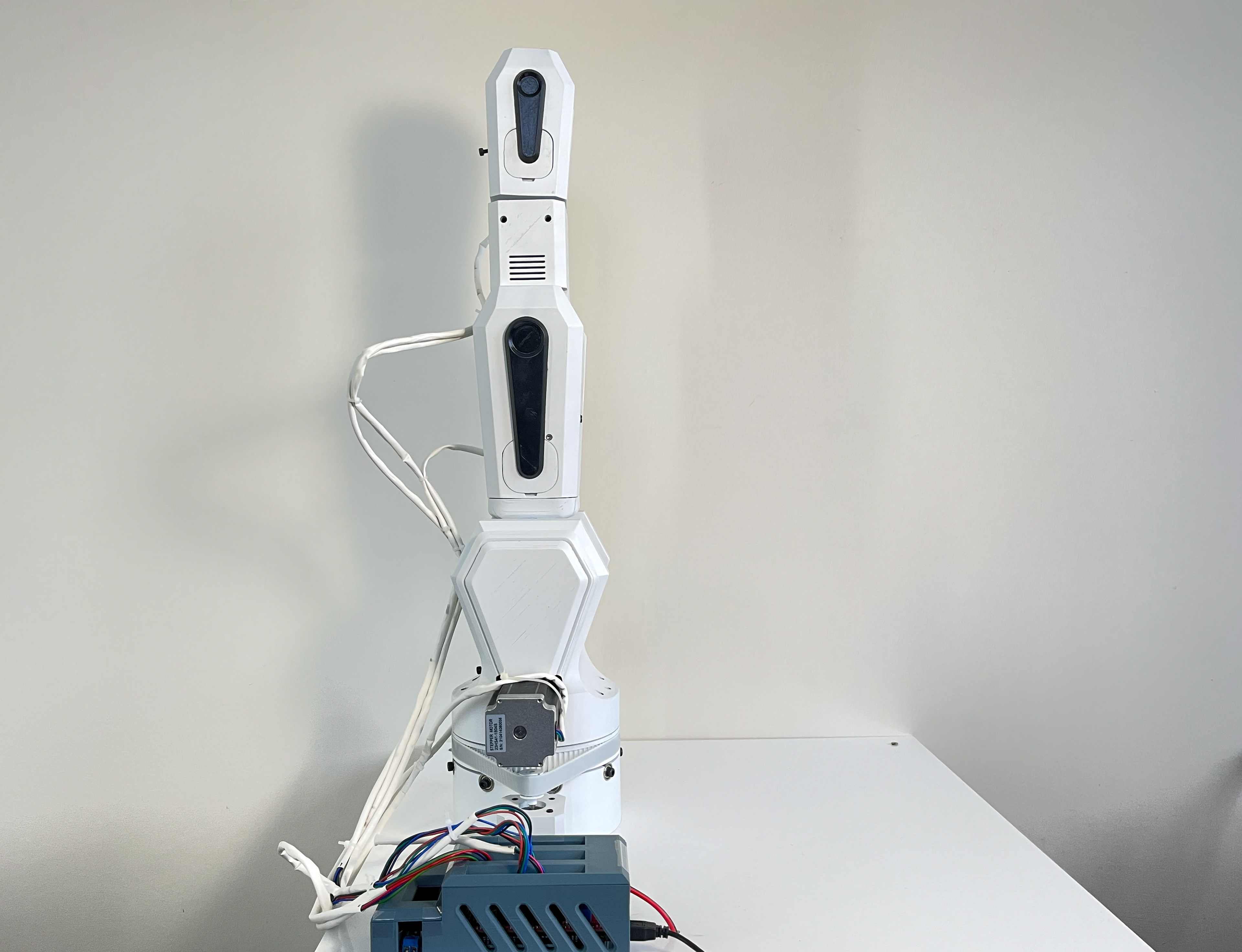
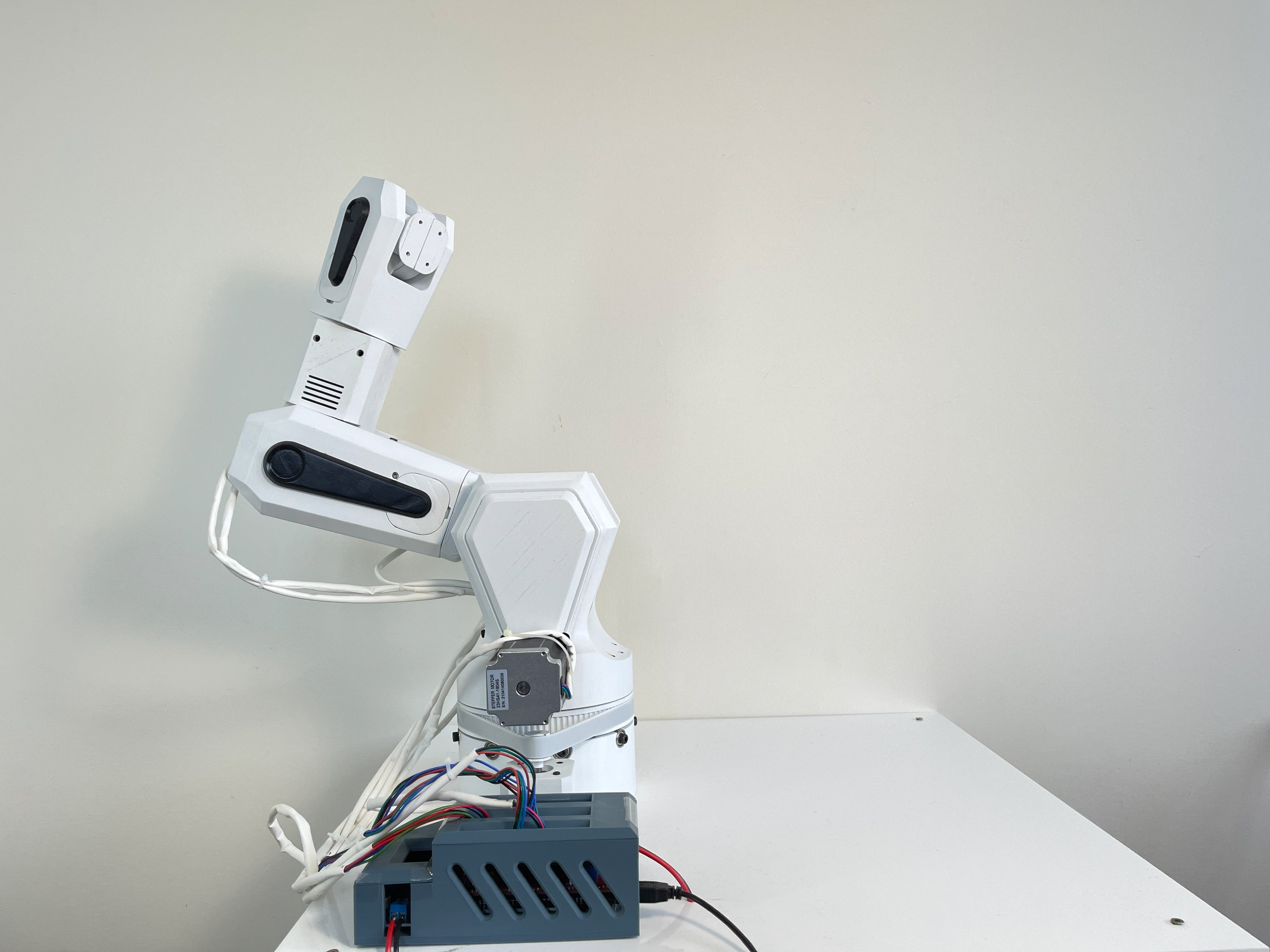
This project ended in the successful completion of a fully working 5 axis robotic arm which entailed a more compact form for electronics by reducing the size down by 47% and a more robust well mechanically improved design that's reliable. Further knowledge was gained on mechanical components, electronics, and having a deeper knowledge of building robotic systems.